What Is a Smart Factory? Key Components & 4 Levels of Evolution
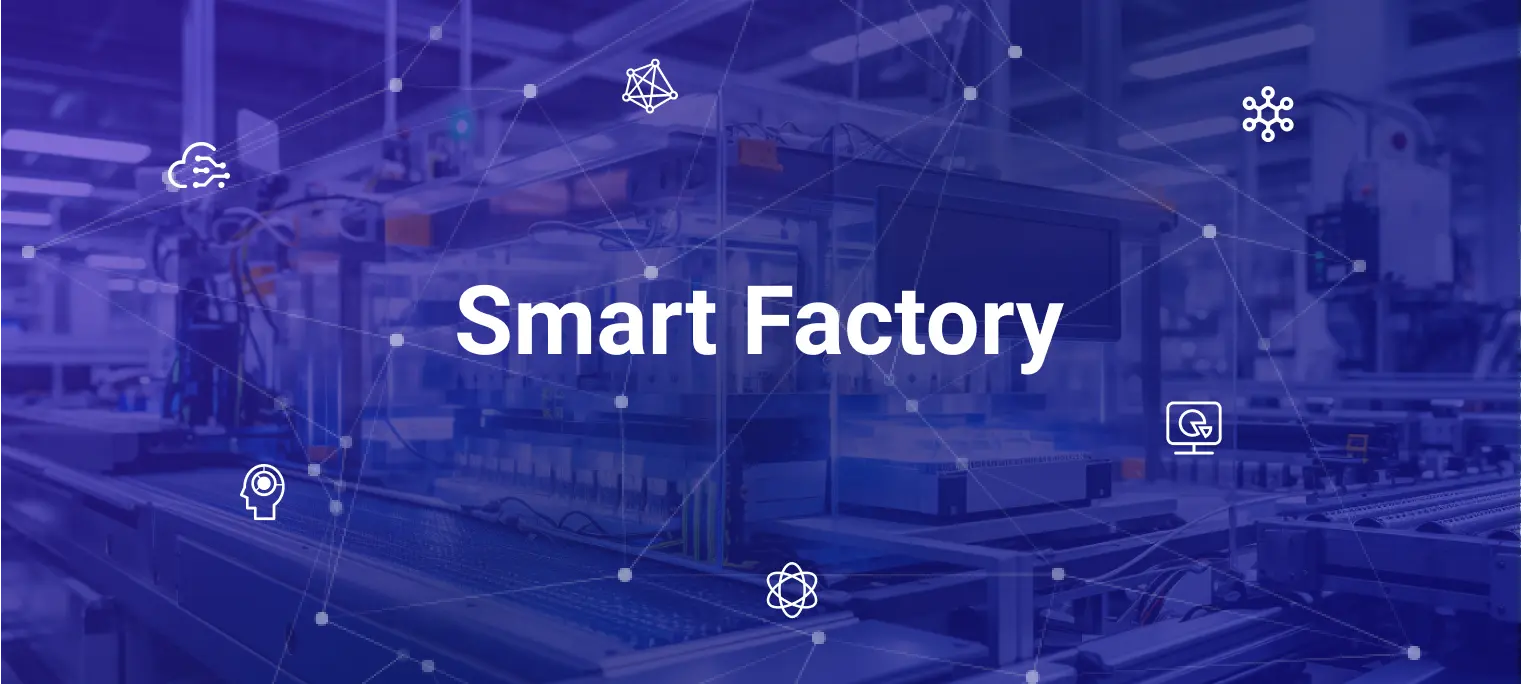
Table of Contents
A smart factory, in its simplest form, is a highly digitized and connected production facility that relies on smart manufacturing. It is the embodiment of the Fourth Industrial Revolution, often referred to as Industry 4.0. The essence of a smart factory is its ability to evolve, adapt, and self-optimize. It seamlessly integrates the physical and digital worlds, using technology to improve processes, reduce waste, and increase productivity.
Imagine a factory where machines communicate with each other, diagnose their own maintenance needs, and automatically adjust production schedules and resources to meet changing demands. A smart factory is a facility where real-time data and predictive analytics drive decision-making, eliminating guesswork and improving efficiency.
By leveraging digital technologies such as Industrial Internet of Things (IIoT), big data and analytics, robotics, and cloud computing, a smart factory not only transforms manufacturing processes but also redefines the very concept of manufacturing itself.
Key Components of a Smart Factory
1. Industrial IoT
The Industrial IoT (IIoT) is the backbone of a smart factory. It involves the use of sensors, machines, and other devices interconnected through a network. These devices continuously collect and exchange data, enabling real-time monitoring and control of the manufacturing processes. This interconnectivity allows for unprecedented visibility into every aspect of the factory, from supply chain to production line, enabling more informed decision making.
Furthermore, IIoT devices can communicate with each other, allowing for machine-to-machine (M2M) interaction. This means machines can autonomously adjust to changing conditions, increasing efficiency and reducing downtime. By leveraging IIoT, smart factories can achieve a level of automation and self-management previously unimaginable.
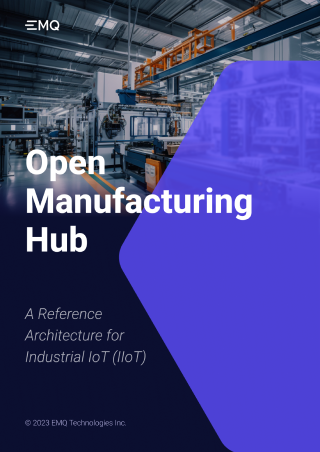
2. Big Data and Analytics
In a smart factory, massive volumes of data are generated. This is where big data and analytics come into play. They provide the means to collect, store, and analyze this vast amount of information, turning raw data into actionable insights.
Predictive analytics, for instance, can identify patterns and trends in the data, allowing for proactive maintenance and preventing equipment failures before they occur. Similarly, prescriptive analytics can offer recommendations based on the data, guiding decision-making and optimizing production processes.
3. Messaging Protocols
Messaging protocols are essential in a smart factory environment, ensuring efficient and secure communication between devices. A smart factory cannot function without a robust internal communication backbone. MQTT (Message Queuing Telemetry Transport) and AMQP (Advanced Message Queuing Protocol) are two of the most widely used messaging protocols in smart factories.
MQTT is a lightweight messaging protocol designed for low-bandwidth, high-latency, or unreliable networks. Its publish/subscribe model makes it ideal for IIoT applications, where a massive number of devices need to communicate without establishing a direct connection. For instance, sensors in remote locations can send data to a central server using MQTT, even under challenging network conditions. MQTT's lightweight nature ensures that it uses minimal power, crucial for battery-operated devices.
AMQP, on the other hand, is an open standard messaging protocol that supports a range of messaging patterns. It guarantees message delivery, ensuring that no data is lost in transmission. This becomes vital in a manufacturing scenario where a missed message can lead to significant operational disruptions. AMQP's layered architecture makes it adaptable to various applications, from simple point-to-point messaging to complex routing and transformation tasks.
Learn more in our detailed guide to AMQP vs. MQTT
4. Robotics and Automation
Robotics and automation are key pillars of a smart factory. They allow for the automation of repetitive tasks, leading to increased productivity and improved quality. Robots can work around the clock, reducing downtime and boosting output.
Moreover, advanced robotics equipped with AI and machine learning capabilities can perform complex tasks with precision and consistency. They can learn from their experiences, improving their performance over time. Coupled with IIoT, robots in a smart factory can communicate with other machines, adjusting their actions based on real-time data, further enhancing efficiency.
5. Cloud Computing
Cloud computing provides the infrastructure needed to support the vast amount of data generated in a smart factory. It offers scalable and flexible storage solutions, enabling the factory to grow and adapt as needed. Additionally, it allows for real-time access to data from anywhere, facilitating remote monitoring and control.
Cloud computing also enables the integration of different systems and technologies, fostering collaboration and information sharing. This interconnectedness is crucial in a smart factory, where seamless communication between machines, systems, and people is key to maximizing efficiency.
Four Levels of Smart Factories
Industry experts have defined four levels of smart factory evolution.
1. Basic Data Availability
The first level of a smart factory revolves around basic data availability. At this stage, the factory is equipped with sensors and other IIoT devices that collect and transmit data. This data is then stored and made available for analysis. The focus here is on data acquisition and storage, providing a foundation for further advancement.
2. Proactive Data Analysis
The second level involves proactive data analysis. With the data now available, predictive analytics can be employed to identify patterns and trends. This allows for proactive decision-making, such as scheduling maintenance before a machine breaks down. At this level, the factory begins to leverage the power of big data and analytics, using data not just for monitoring but also for prediction and optimization.
3. Active Data
The third level, active data, takes this a step further. Here, the factory not only analyzes data but also uses it to autonomously adjust operations in real-time. For instance, if a machine detects an increase in demand for a certain product, it can automatically adjust production schedules and resources to meet this demand. This level of responsiveness and adaptability is a defining feature of a smart factory.
4. Action-Oriented Data
The fourth and final level is action-oriented data. At this stage, the smart factory fully realizes the potential of IIoT, with big data and analytics, robotics, advanced automation, and cloud computing. It not only collects, analyzes, and responds to data, but also learns from it. Using machine learning and AI, the factory can continuously improve its operations, becoming more efficient, productive, and resilient over time.
Benefits of Smart Factories
Increased Efficiency and Productivity
Among the most appealing benefits of smart factories is the promise of increased efficiency and productivity. By leveraging advanced technologies such as the Internet of Things (IoT), artificial intelligence (AI), and machine learning, smart factories can automate routine tasks, freeing up human employees to focus on more complex and value-added activities.
Moreover, these technologies also enable real-time monitoring and analytics, providing manufacturers with valuable insights into their operations. This allows them to identify bottlenecks, predict equipment failures, and make informed decisions to optimize performance. Thus, the smart factory's ability to operate and adapt autonomously not only boosts productivity but also enhances operational efficiency.
Enhanced Customization and Personalization Capabilities
The second benefit that smart factories offer is the ability to deliver highly customized and personalized products. In the traditional manufacturing setup, mass production was the norm, with little room for customization. However, with the advent of smart factories, the game has changed.
Advanced technologies like 3D printing and digital twin technology make it possible to create highly customized products on a large scale. This not only meets the growing consumer demand for personalized products but also gives manufacturers a competitive edge in the market. As such, smart factories are redefining the concept of mass customization.
Improved Quality and Reduced Errors
Smart factories also play a crucial role in improving product quality and reducing errors. By leveraging technologies such as AI, machine learning, and predictive analytics, smart factories can monitor and analyze the entire manufacturing process in real-time.
This allows for the early detection of defects or anomalies, enabling manufacturers to take corrective action before the product reaches the final stage of production. Consequently, this results in fewer product defects, reduced waste, and improved overall product quality.
Better Resource Management and Waste Reduction
Better resource management and waste reduction are other significant benefits of smart factories. With the help of IoT sensors and advanced analytics, smart factories can monitor the usage of resources in real-time, enabling manufacturers to optimize their resource allocation and reduce waste.
For instance, smart factories can track the usage of energy, water, and raw materials, allowing for more efficient utilization. This not only leads to significant cost savings but also contributes to environmental sustainability.
Enhanced Safety Measures
By leveraging technologies such as IoT, AI, and robotics, smart factories can create a safer working environment. For instance, robots can be used to perform hazardous tasks, thereby reducing the risk of accidents. Moreover, IoT sensors can detect potential safety hazards and alert employees in real-time. As such, smart factories not only enhance productivity and efficiency but also prioritize employee safety.
Key Challenges in Implementing Smart Factory Solutions
High Initial Investment Costs
Despite their numerous benefits, implementing smart factory solutions is not without challenges. One of the major hurdles is the high initial investment cost. The transition to a smart factory requires significant financial resources to acquire and implement advanced technologies such as IoT, AI, and robotics.
However, it's essential to view these costs as an investment rather than an expense. Over time, the increased efficiency, productivity, and cost savings resulting from smart factory solutions can yield a high return on investment.
Integration with Legacy Systems
Another challenge is the integration of smart factory solutions with existing legacy systems. Many manufacturers have been operating with the same systems and processes for years, making it difficult to implement new technologies.
Yet, with the right approach and strategic planning, it's possible to integrate smart factory solutions without disrupting the existing operations. This often involves a phased approach, gradually introducing new technologies and allowing employees time to adapt.
Skills Gap and the Need for Workforce Training
The third challenge is the skills gap and the need for workforce training. The transition to a smart factory requires employees to have a new set of skills, including digital literacy, data analysis, and the ability to work with advanced technologies.
To address this challenge, manufacturers must invest in training and development programs. This not only equips employees with the necessary skills but also helps to build a culture of continuous learning and innovation.
Data Security and Privacy Concerns
Data security and privacy are other critical concerns when implementing smart factory solutions. With the increased use of digital technologies and the generation of vast amounts of data, manufacturers must ensure that they have robust security measures in place to protect sensitive information.
This involves implementing security protocols, encrypting data, and regularly updating systems to guard against cyber threats. Additionally, manufacturers must comply with data privacy regulations to protect the personal information of employees and customers.
Simplifying Smart Factory Connectivity with EMQX
EMQ provides Neuron, a lightweight connectivity server for industrial dataops and data-centric automation, tightly integrated with our industry-leading MQTT broker. Neuron provides several significant benefits for IIoT, simplifying connectivity, enhancing data integration, and enabling real-time communication and analytics.
If you are a managing an IIoT deployment, EMQX and Neuron can help with:
- IT Connectivity: EMQX broker offers a wide range of data bridges, facilitating seamless integration with over 40 cloud services and enterprise systems. This enables instant access to data across diverse applications, reducing the cost and complexity of custom bridge development. EMQX supports integration with popular databases like MySQL, PostgreSQL, MongoDB, and more, as well as technologies like Redis, Oracle, SAP, and Kafka. This rich set of connectors ensures efficient IT connectivity and data exchange within the IIoT ecosystem.
- OT Connectivity: Neuron serves as a protocol gateway, providing a comprehensive set of industrial connectivity options essential for successful IIoT deployments. With support for over 30 industrial protocols such as Modbus, Ethernet/IP, Profinet I/O, OPC-UA, IEC104, BACnet, and more, Neuron enables seamless communication with various devices and systems across the operational technology (OT) landscape. Whether it's PLCs, building automation systems, CNC machines, or robotics, Neuron offers a powerful range of drivers to ensure reliable OT connectivity and data acquisition.
- Unified Namespace: EMQX and Neuron can be used together to create a unified namespace for industrial IoT applications. A unified namespace is a common naming convention for MQTT topics that allows devices and applications to communicate with each other regardless of location or protocol. All devices and applications use the same MQTT topic hierarchy based on a common set of naming conventions and data models. This allows devices to discover and communicate with each other without the need for complex routing or translation mechanisms.
- Data Distribution: By leveraging the EMQX brokers high speed throughput and low latency capabilities, OMH can provide multiple location high speed data replication. High-speed replicating data across multiple manufacturing locations ensures consistency in the data shared among different locations. When data is replicated, each location has access to the same set of information, ensuring that decisions and actions are based on the most up-to-date and synchronized data. This promotes uniformity in operations, reduces discrepancies, and enables standardized processes across all sites.
- Interoperability and Scalability: EMQX broker and Neuron gateway can be used together to ensure the interoperability and scalability of the manufacturing information infrastructure by establishing a more flexible and interconnected data exchange approach. A centralized data repository is established to store and manage all the data collected from various levels of the information systems. This repository acts as a central hub where data from field-level devices, SCADA, MES and ERP is consolidated.
- Edge and Cloud Stream Processing: Neuron gateways may offer edge computing capabilities, enabling data preprocessing and filtering at the edge of the network. This reduces latency, conserves bandwidth, and optimizes data transmission to the central MQTT broker. Once the data is in the EMQX broker, it can be further processed, analyzed, and integrated with other systems. This could involve data storage in databases, real-time analytics, or forwarding the data to cloud platforms for further processing.
- MQTT Sparkplug: EMQX is a popular MQTT broker that supports the Sparkplug protocol, while Neuron is an industrial IoT platform that can be used to collect data from industrial devices and generate Sparkplug messages for applications. Neuron can collect the data from the devices and publish Sparkplug messages to the EMQX broker based on the data by reporting changes. EMQX will forward the messages to the application that subscribes to the relevant Sparkplug topic.
- OPC UA over MQTT: Neuron, as an industrial connectivity gateway, could have been updated to include native support for OPC UA over MQTT. Any data formats can be re-organized into OPC UA formats and sent over MQTT to EMQX broker that can handle large-scale OPC UA over MQTT deployments with high throughput and reliability to the subscribers.
Learn more in our detailed guide to MQTT sparkplug
By combining the capabilities of EMQX as an MQTT broker with Neuron's industrial connectivity gateway, IIoT connectivity is streamlined, enabling seamless communication between industrial devices and backend systems. The integration of these components simplifies data exchange, enhances data processing, and optimizes IIoT deployments for improved efficiency, reliability, and real-time decision-making in industrial applications.
Learn more about Neuron: The Industrial IoT Connectivity Server