Smart Manufacturing Explained: Basics, Use Cases & Best Practices
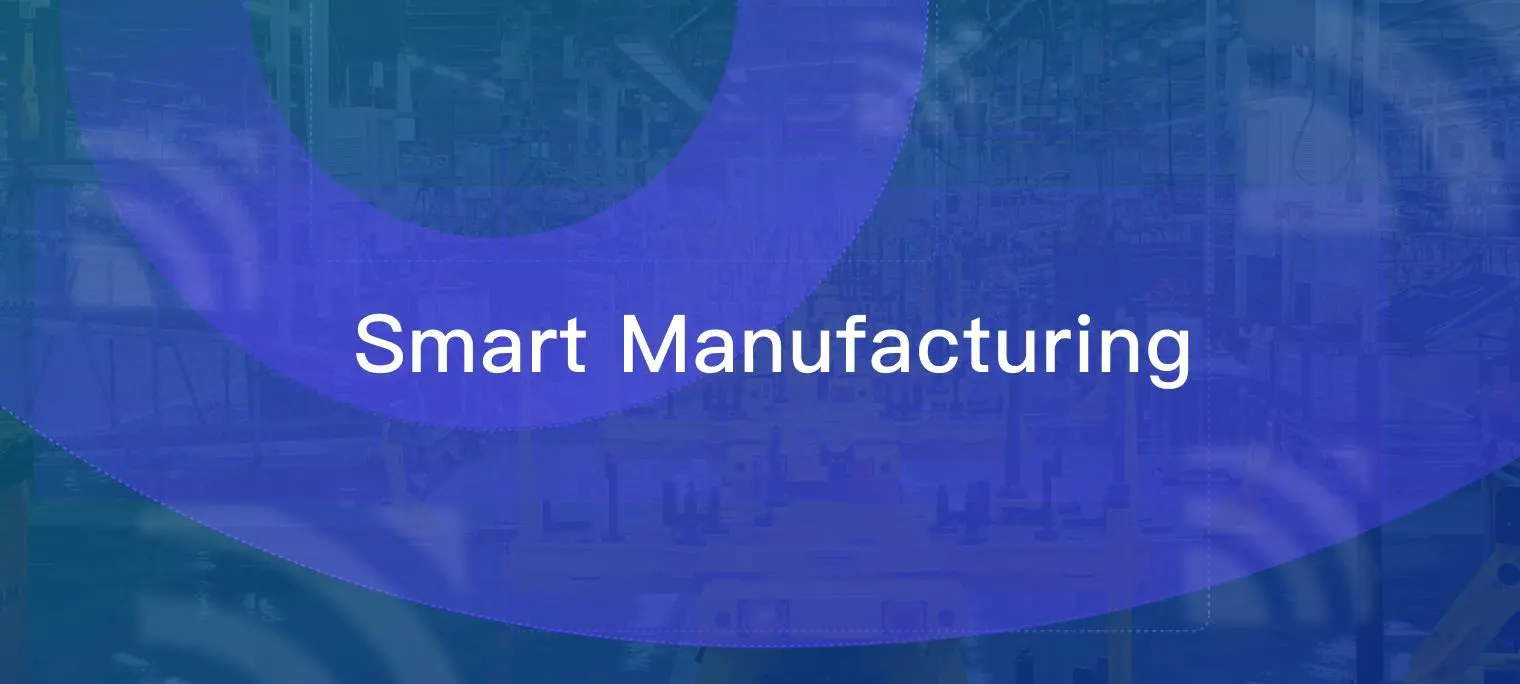
Table of Contents
What Is Smart Manufacturing?
Smart manufacturing refers to the integration of advanced digital technologies—such as IoT, AI, big data analytics, and cloud computing—into every layer of the manufacturing process. It transforms traditional factories into intelligent systems that can monitor, analyze, and optimize production in real time.
Smart manufacturing combines industrial automation and information technology. It integrates physical machinery with networked sensors and software, used to predict, control and improve performance. The aim is to create a self-regulating system that optimizes productivity, reduces waste, and increases overall operational effectiveness.
At its core, smart manufacturing is about connectivity and intelligence. It brings together all aspects of the manufacturing process, from supply chain management to production to customer service, under a single digital umbrella. This holistic approach offers a cohesive view of the entire operation, facilitating more informed decision-making and fostering innovation.
Smart Manufacturing Use Cases
Predictive Maintenance
Predictive maintenance involves collection of data from sensors embedded in manufacturing equipment, and analyzing it to predict when a machine might fail or require maintenance. This allows companies to fix problems before they occur, reducing downtime and increasing productivity.
For example, a manufacturing plant might use vibration sensors on its machinery to detect abnormal patterns that could signal an upcoming failure. The system would then alert the maintenance team, allowing them to address the issue before it causes a breakdown. Predictive maintenance not only helps prevent costly disruptions but also extends the lifespan of equipment.
Real-Time Monitoring and Control
Real-time monitoring and control involves the continuous tracking of production processes and the ability to make instantaneous adjustments as necessary. This feedback loop allows for unprecedented control over manufacturing operations.
For example, a beverage company can use real-time monitoring to track the filling of its bottles. If the system detects a deviation from the desired fill level, it can immediately adjust the flow rate to correct the error. This level of control reduces waste, ensures consistency, and enhances product quality.
Product Quality Assurance
Smart manufacturing also plays a critical role in product quality assurance. By leveraging data and analytics, manufacturers monitor and control every step of the production process, from raw material selection to final product testing.
For instance, a car manufacturer might use smart manufacturing technologies to ensure that every vehicle it produces meets stringent quality standards. Sensors might monitor variables such as temperature, pressure, and speed during the assembly process, with any anomalies immediately flagged for investigation. This ensures that only top-quality products leave the factory.
Supply Chain Optimization
By digitizing and integrating all elements of the supply chain, manufacturers can achieve greater transparency, efficiency, and resilience. Supply chain optimization improves efficiency, minimizes waste, and promotes sustainability in the manufacturing sector.
Consider a clothing manufacturer that uses a smart manufacturing system to track its supply chain. The system might monitor factors such as raw material availability, production rates, and delivery times, providing real-time insights that enable the manufacturer to optimize its operations.
Cost Savings
By automating processes and enhancing efficiency, manufacturers can significantly reduce their operational costs. Smart manufacturing technologies can also monitor the utilization of resources, helping manufacturers to optimize their use and reduce waste.
For example, a steel production company may use smart manufacturing technologies to monitor energy consumption in real-time, identifying areas of excessive energy use and inefficiency. By adjusting these processes, the company can lower its energy costs, reduce its carbon footprint, and improve its overall operational efficiency.
Industrial Safety
Safety is a top priority in any manufacturing environment, and smart manufacturing can significantly enhance it. Automation and robotics can handle dangerous tasks, reducing the risk of accidents and injuries. Additionally, smart manufacturing systems can monitor the working conditions and alert operators about potential hazards, helping to create a safer workplace.
For instance, a chemical manufacturing plant may employ smart sensors that continuously monitor the environment for hazardous gas leaks. Should such a leak occur, the system would immediately alert workers and initiate emergency protocols, preventing potential accidents and ensuring worker safety.
Personalization and Customization
Smart manufacturing also enables personalization and customization on a scale that was previously unimaginable. With advanced technologies like 3D printing and IoT, manufacturers can produce customized products efficiently and cost-effectively.
Take for example, a furniture manufacturer using smart manufacturing techniques. Leveraging 3D printing technology, the manufacturer can create unique, custom-designed furniture pieces based on customer specifications. Customers can personalize their designs, choosing the dimensions, materials, and finishes, and the system then produces the pieces to exact specifications. This enables manufacturers to offer personalized products without sacrificing efficiency or increasing costs.
Core Technologies Behind Smart Manufacturing
Internet of Things (IoT)
The internet of things (IoT) is a key technology underpinning smart manufacturing. It involves the interconnection of physical devices—from machinery to sensors to software—over the internet. This connected ecosystem allows for the collection, exchange, and analysis of data, enabling real-time monitoring, control, and optimization of manufacturing processes.
Artificial Intelligence (AI) and Machine Learning (ML)
Artificial intelligence (AI) and machine learning (ML) enable systems to learn from data, identify patterns, and make decisions with minimal human intervention. This capacity for autonomous learning and decision-making is critical for predictive maintenance, product quality assurance, and supply chain optimization.
Big Data Analytics
Big data analytics involves the analysis of large volumes of data to uncover hidden patterns, correlations, and insights. In the context of manufacturing, this can lead to improved operational efficiency, product quality, and customer satisfaction.
Robotics and Automation
Robots can perform repetitive tasks more accurately and efficiently than humans, while automation can streamline and optimize production processes. Combined with AI and ML, robotics and automation can create truly autonomous manufacturing systems.
Cloud Computing
Finally, cloud computing is a key enabler of smart manufacturing. It provides a scalable, flexible, and cost-effective platform for storing and processing data. In the manufacturing sector, cloud computing enables real-time data sharing and collaboration, facilitating more efficient and effective decision-making.
What is the Industrial Internet of Things (IIoT)?
The Industrial Internet of Things (IIoT) is a significant facet of smart manufacturing. It refers to the interconnectedness of industrial equipment, facilities, personnel, and processes. By connecting devices and systems in the industrial environment, valuable data can be captured, analyzed, and utilized to improve operational efficiency and productivity.
IIoT is an expansion of the IoT, tailored to the industrial sector. It includes machine-to-machine communication, enabling systems to interact and collaborate, creating an intelligent network of machines and people that can monitor, collect, exchange, and analyze data. This data is then utilized to improve manufacturing processes, enhance supply chain management, and make the overall operation more efficient and effective.
For instance, in a factory environment, sensors placed on manufacturing equipment can collect a variety of data such as operating temperature, speed, vibration, and more. This data can be analyzed in real-time to detect anomalies that may indicate potential malfunctions or inefficiencies. By detecting such issues early, predictive maintenance can be performed, preventing machine failure, reducing downtime, and saving costs.
In the context of supply chain management, IIoT can provide real-time visibility into inventory levels, production status, and transportation logistics, enabling manufacturers to optimize their supply chains, reduce waste, and improve customer service.
By creating a network of intelligent systems that can communicate and make decisions, IIoT is helping to create smarter, more efficient, and more flexible manufacturing environments. It's a vital part of the digital transformation that's sweeping the industrial sector, unlocking new levels of performance and productivity.
Best Practices for Implementing Smart Manufacturing Systems
The following best practices can help you implement smart manufacturing more effectively.
Develop a Clear Strategy
Implementing smart manufacturing is not just about adopting new technologies. It requires a clear strategy that aligns with the organization's goals and objectives. This strategy should outline how smart manufacturing will enhance the organization's operations, what technologies will be used, and how they will be integrated into the existing processes.
It's also crucial to involve all stakeholders in the development of this strategy, including management, employees, and suppliers. This ensures buy-in from all parties, facilitating a smooth implementation.
Ensure Data Security
Data is the lifeblood of smart manufacturing, but it also presents significant security risks. Therefore, ensuring data security should be a top priority when implementing smart manufacturing systems. This involves adopting robust cybersecurity measures, such as firewalls, encryption, and intrusion detection systems.
It's also essential to regularly update these security measures to protect against evolving threats. Additionally, manufacturers should educate their employees about the importance of data security and provide them with the necessary training to prevent security breaches.
Cultivate Skills and Expertise
Smart manufacturing requires a new set of skills and expertise. Therefore, manufacturers should invest in training and development programs to equip their workforce with the necessary capabilities. This may involve providing training on new technologies, data analysis, and cybersecurity.
Manufacturers should also consider partnering with educational institutions or industry bodies to develop specialized training programs. By cultivating skills and expertise, manufacturers can ensure that their workforce is ready to harness the full potential of smart manufacturing.
Implement in Phases
Implementing smart manufacturing is a complex process that can be overwhelming. Therefore, it's advisable to implement it in phases. This allows manufacturers to test the effectiveness of the new technologies and processes, learn from their mistakes, and make necessary adjustments.
It also reduces the risk of disruption to the existing operations. Manufacturers should start with small pilot projects, and once they are successful, they can scale up the implementation.
Regularly Review and Adjust
Smart manufacturing is not a one-time project, but a continuous journey. Therefore, manufacturers should regularly review their smart manufacturing systems and make necessary adjustments. This involves monitoring the performance of the systems, assessing their impact on the operations, and identifying areas for improvement.
Manufacturers should also stay abreast of the latest advancements in smart manufacturing technologies and incorporate them into their systems. Regular review and adjustment ensure that the smart manufacturing systems remain effective and relevant in the ever-changing manufacturing landscape.
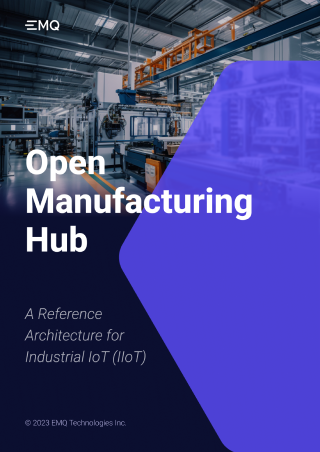
IIoT Connectivity for Smart Manufacturing with EMQX and NeuronEX
As smart manufacturing evolves, data-driven intelligence is no longer optional—it’s essential. EMQ provides a future-ready platform that combines high-performance MQTT messaging and industrial connectivity with AI-first architecture. This enables manufacturers to move from simple automation to intelligent decision-making at both the edge and the cloud.
EMQX: MQTT+AI Platform for Real-Time Data Streaming
EMQX is a leading MQTT platform built for high-throughput, low-latency communication. It enables reliable messaging between industrial devices, control systems, and cloud platforms—forming the communication backbone of IIoT.
- Real-time Data Exchange: EMQX handles millions of concurrent connections, making it ideal for large-scale smart manufacturing environments.
- Cloud Integration: EMQX supports integration with AWS, Azure, and Google Cloud, enabling centralized analytics and predictive maintenance workflows.
- Security and Reliability: EMQX offers TLS encryption, authentication, and access control to safeguard sensitive industrial data.
- AI/ML Integration: Analyze data in motion, identify trends, automate processes, gain real-time insights, and make data-driven decisions with stream processing and AI/ML on the factory floor.
NeuronEX: Industrial Gateway for Unified Connectivity and Edge Intelligence
NeuronEX connects industrial devices running on legacy protocols (Modbus, OPC UA, EtherNet/IP, etc.) to modern data platforms using MQTT. It bridges the gap between traditional OT equipment and modern IoT systems.
- Protocol Translation: Seamlessly converts industrial protocols into MQTT for real-time communication with cloud or edge platforms.
- Edge Processing and AI Inference: Executes rule logic and AI models at the edge, enabling low-latency responses and localized decision-making.
- Scalable Architecture: Easily expands from pilot projects to full-scale deployments with thousands of connected devices.
Together, EMQX + NeuronEX enable manufacturers to:
- Achieve real-time visibility across machines, processes, and systems
- Integrate CNCs, PLCs, and industrial robots into smart workflows
- Streamline predictive maintenance and production analytics
- Build secure, flexible IIoT infrastructure with cloud and edge support
Whether you're building a smart production hub or upgrading legacy equipment, EMQ's solution offers the performance, flexibility, and interoperability needed to accelerate your smart manufacturing journey.
Learn more:
- Smart Manufacturing Solution
- Software-Defined, AI-First: A Smart Manufacturing Revolution
- Open Manufacturing Hub: A Reference Architecture for Industrial IoT (IIoT)